Alba was recently approached by Robotiq, a robotic integrator, to help with a robotic palletizing project where a variety of bucket sizes needed to be palletized. The buckets contained frosting for a bakery company and needed to be palletized prior to shipment on either GMA or CHEP style pallets.

The bakery aimed to automate the process of palletizing, moving away from the manual method of stacking buckets on each side of a pallet. Instead, they wanted to use a robotic system to palletize directly onto the pallet on the conveyor. This company also wanted to avoid allocation of their existing staff to place empty pallets onto the conveyor.
Alba supplied a pallet dispenser to dispense empty pallets and convey them to a robotic pallet build zone where Robotiq use their AX30 palletizing solution. The AX30 is a solution built around the UR30 collaborative robot arm, which is Universal Robot’s highest payload arm, able to palletize up to 77 lb. (35 kg).
For this application, the customer needed to move 57 lb. of material per robot pick. While the UR30 has limited reach compared to lower payload robots, Robotiq compensated for this with a "seventh axis" in their solution, allowing the robot to move up and down the "Z" axis to pick and place at its optimal height. Alba provided the conveyor system that spans from the dispenser to the pallet build zone and extends to the fork truck pick-up area. The conveyor was designed with the cobot’s limited reach in mind.
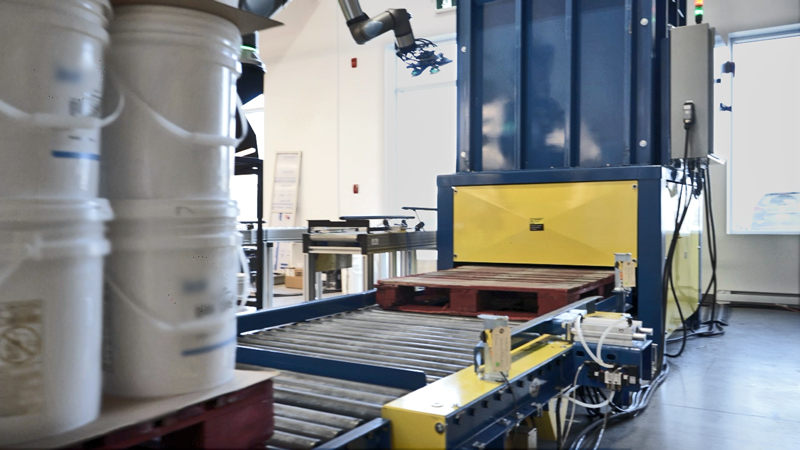 |

The build zone consisted of a CDLR (chain driven live roller) conveyor that conveyed empty pallets to a blade stop and then while the pallet was stopped, push the empty pallet to square it against a backstop. This allowed the pallet to be located in a position the robot could identify to begin its palletizing process. In the end, full pallets weighing a maximum of 2,736 lb. would convey to the end of the line for pick-up at a rate of 15 pallets per hour. Alba supplied all the necessary photo-eyes and proximity switches.
When the robot completes loading a pallet, a signal is sent to the pallet dispenser to send the completed pallet downstream to a fork truck pick-up conveyor and to stage another empty pallet at the build zone. The completed pallet would then be picked up by a fork truck before the next pallet build is completed.
The pick-up conveyor was designed for side unloading by a fork truck and featured an ultrasonic sensor to detect whether the fork truck was properly positioned for pick-up. Since there were only two conveyors downstream of the dispenser, Alba also provided the base controls package for this system. This panel included a PanelView 800 HMI (Human-Machine Interface) touchscreen to control the functions of the dispenser, the conveyors at the build zone, and the pick-up zone.
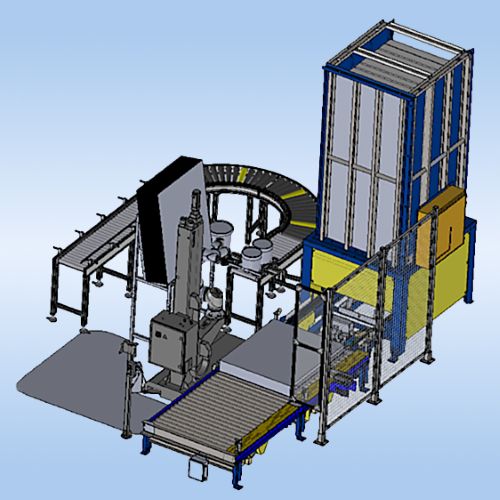 |
|
This system allowed for the conveyor cell to operate autonomously during normal operations, with the only exception being the fork truck driver unloading full pallets of finished product. Alba provided zoned conveyors for precise accumulation and repeatable product presentation to the robot. Robotiq added an interlayer sheet rack for picking and placing two sheets per pallet during the palletizing sequence and provided the safety scanners, wire partitions, and light curtains to separate the palletizing area from the fork truck aisle.
Contact Alba today to see how our conveyors and solutions can take your project to the next level and put the icing on the cake! Contact us online at www.albamfg.com or contact one of our knowledgeable salespeople today at (866) 252-2634. |

Conveyor/Product Specifications |
• |
Automated Pallet Dispenser with Integral 2-Strand Drag Chain Conveyor and Electric/Hydraulic Scissor Lift at its Base. |
• |
All Devices within the Dispenser Wired back to a Control Panel with included Allen-Bradley CompactLogix PLC and PanelView800 7" Color Touchscreen HMI and Ethernet Switch for Connection between PLC and HMI. Primary Power was 460/3/60 and Control Power was 24VDC. |
• |
Push Buttons on Panel also included Emergency Stop, E-Stop Reset, Start Button, Stop Button, and Manual Lift Up/Down 3-Position Spring-to-Center Selector Switch. |
• |
Control Panel also included a 3-Color Stack Light, (2) Control Relay Handshake Signals, and UL Certification of Control Panel. |
• |
Model 251140-3.25-44 CDLR Conveyor (Pallet Build Zone) with ABEC-1 "PFR" Precision Bearings, Baldor Super "E" Motor, QD Motor Connector, 30 FPM @ 60 Hz., Supports for 18" Top of Roller Elevation. |
• |
Build Zone included a Pneumatic Operated Blade Stop with Two (2) Proximity Switches, 24VDC Double Solenoid Valve, and Filter/Regulator with Gauge. |
• |
Build Zone was Equipped with an Empty Pallet Pneumatic Pusher with Two (2) Proximity Switches (Extend/Retract) and a 24VDC Double Solenoid Valve. |
• |
Model 251140-3.25-44 CDLR Conveyor (Fork Truck Pick-up Zone) with ABEC-1 "PFR" Precision Bearings, Baldor Super "E" Motor, QD Motor Connector, 30 FPM @ 60 Hz., Supports for 18" Top of Roller Elevation. |
• |
Pick-up Zone included an Ultrasonic Sensor Mounted on the Side of the Conveyor, a Fixed End Stop, and a Formed Backstop. |
• |
Alba provided a Junction Box on the Pallet Build Zone Conveyor for Pre-wiring of all Conveyors and Devices Outside of the Dispenser. |
• |
All Conveyors included the appropriate Retro-reflective Photo-eyes and were Pre-wired back to the Dispenser Control Panel. |

More About Robotiq |
Robotiq’s mission is to free humans’ hands from repetitive tasks. Robotiq automates manual tasks with cobot workcells and components, following lean robotics principles. The company’s solutions boost productivity, empower workers, and adapt quickly to changing production needs – minimizing downtime and keeping manufacturers competitive. From palletizing to assembly, Robotiq streamlines automation with easy-to-use software and global installation support. |
|