Alba Manufacturing recently collaborated with Greenbridge, a trusted systems integration partner and OEM (Original Equipment Manufacturer) of strapping and wrapping machines, to deliver a customized material handling system for the final packaging of scroll compressors used in both commercial and residential air conditioning systems.
The project required a conveyor system to transport pallets of manually palletized scroll compressors from a pack-out area to a downstream strapping and wrapping line. The system needed to handle loads up to 2,700 lb. and accommodate two different types of pallets – a 4-way double-winged pallet and a larger CHEP-style pallet.
Key Challenge
The primary challenge in the application was to maintain accessibility to the manual packing area. The redesign ensured that this area remained fully accessible by avoiding the installation of a permanent conveyor line. This was crucial to enable the retrieval of components and pallets from this area during occasional line stoppages, without any obstructions.
Alba’s Solution
Alba collaborated with Greenbridge to address the project needs by supplying six Chain-Driven Live Roller (CDLR) Conveyors for manual palletizing. To streamline the movement of finished pallet loads from the manual palletizing area to further processing stages, Alba implemented a double conveyor top Transfer Car. This transfer car efficiently transported the pallets to another downstream conveyor line using a Drag Chain Conveyor, also provided by Alba. This downstream conveyor facilitated the movement of pallets through two Greenbridge strapping machines and subsequently to a wrapping station, ensuring a seamless flow of operations.
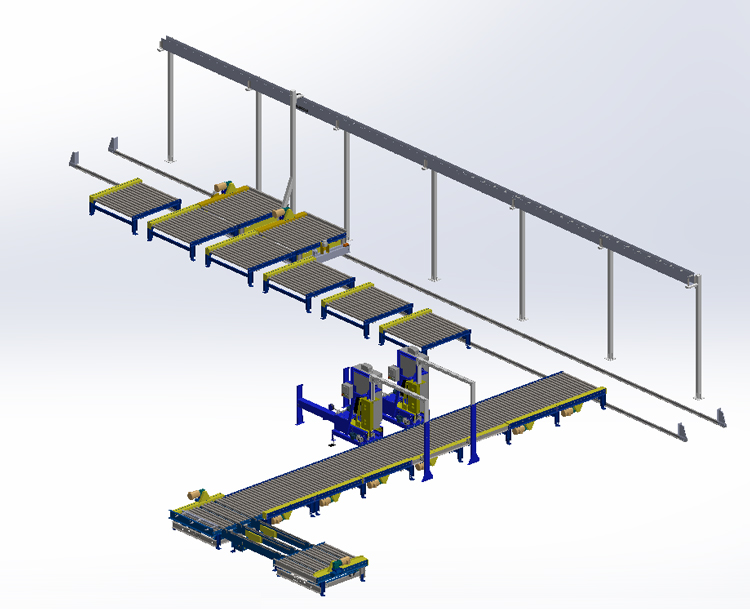
Innovative Design Features
- Smart Laser Sensors: The transfer car was outfitted with advanced smart laser sensors at both the front and back, enhancing precision and safety in navigation.
- Visibility and Audibility Enhancements: Four amber lights were installed at the corners of the car for improved visibility, accompanied by two horns to make the moving T-Car audible, thereby alerting nearby personnel.
- Overhead Energy Chain: To power the T-Car and maintain a safe environment, Alba implemented an energy chain that was strategically positioned overhead. This design choice kept the energy supply out of the way of floor traffic, mitigating any potential safety hazards.
- Support Structure for Energy Chain: The energy chain was supported by floor-mounted posts holding a formed cable tray, in which the energy chain laid and moved as the T-Car traversed back and forth. This setup ensured a clean and organized movement of the cables.
- Elevated Mast Design: The T-Car featured a high mast that extended above the vehicle, routing cables up to the overhead energy chain. This arrangement kept the electrical connections elevated, avoiding interference with pedestrian traffic.
- Embedded Track Design: The tracks for the T-Car were embedded in the floor at the final installation site to minimize trip hazards. This design not only enhanced safety but also preserved the usability of the space.
- Extended Track with Safety Stops: The T-Car operated along a 48-foot-long galvanized track, which included stops at both ends to prevent the car from over-traveling, ensuring additional safety and reliability during operation.
These design features showcased Alba’s commitment to innovative solutions that enhance operational efficiency while prioritizing safety and accessibility.
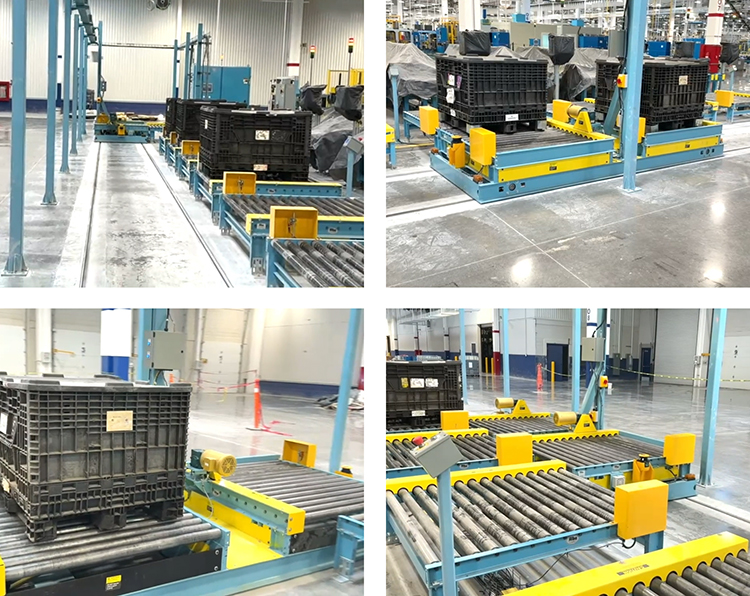
To ensure and verify optimum functionality, this system underwent rigorous testing at Greenbridge before being shipped and installed at the end user’s facility. The successful collaboration between Alba Manufacturing and Greenbridge from start to finish resulted in a robust and reliable system designed to provide long-lasting functionality and service. This project exemplifies how customized solutions can effectively tackle complex material handling challenges.
Click here to review Greenbridge’s YouTube Page.
If you’re seeking dependable and innovative material handling systems, Alba Manufacturing is your go-to partner. We have the expertise to address and resolve your most challenging applications.
Conveyor/Product Specifications
- 46″ x 44″ CHEP Style Pallets
- 43-1/2″ x 43-1/2″ 4-Way Double Winged Pallets
- 2,700-lb. Pallet Loads
- All Conveyors – 45FPM @ 60 Hz.
- Various Model 251140-4-52 CDLR (Chain Driven Live Roller) Conveyors
- Model 251140-4-52 CDLR (Chain Driven Live Roller) Conveyor with Transfer Car Base:
- 3HP Nord Gearmotor with Brake
- 120FPM @ 60 Hz. (Traversing Speed)
- Flanged Track Wheels
- ASCE 30# Rail (Galvanized) x 48′-0″ Long with Wheel Stops
- Two (2) Laser Sensors
- Four (4) Amber Lights
- Two (2) Industrial Horns
- Energy Chain in Formed Cable Tray Supported on Seven (7) Floor Mounted Posts
- Various Model TFT251140-4-3S-52 Thru-Frame Type 90° Transfers
- Model DC-R80-3S 3-Strand Drag Chain Conveyor
About Us
Alba Manufacturing, established in 1973, engineers and designs heavy-duty roller conveyor systems. Our systems consist of chain driven live roller (CDLR), zero pressure accumulation, drag chain, gravity, lift and rotate, pallet stackers and dispensers, turntables, chain transfers and transfer cars. Our corporate office and manufacturing facility is located in Fairfield, Ohio, approximately 30 minutes north of Cincinnati, Ohio.
For more information regarding this application/solution, please contact us via phone at 866.252.2634; via web at www.albamfg.com or via email at RockSolidConveyor@albamfg.com.