Is it whisky, or whiskey? For the non-afficionados, the answer is both. Scottish and Canadian brands are spelled without the letter “e” – all others include the letter “e.”1 Whisky or whiskey is a type of distilled alcoholic beverage made from fermented grain mash. Various grains are used for different varieties, including barley, corn, rye, and wheat. Whiskey is typically aged in wooden casks, which are usually made of charred white oak.
Charring the wood primes the wood, which impacts the spirit’s flavor. It opens the wood up, making it easier for bourbon to extract flavors. It also catalyzes key chemical changes that are essential to the distilling process. Most of the vanilla flavor in whiskey, for example, comes from the breakdown of lignin in oak barrels, which is expedited by charring.2
Our Product
200 Oak, Whiskey Barrel Heads on a 48″ x 48″ Plastic Flat Bottom Pallet Weighing Up to 2,000 lb. Maximum.
We worked closely with our system integrator, Automated Systems International (ASI), who focuses on the whiskey barrel industry. Since ninety-five percent of all bourbon whiskey is produced in Kentucky1, it’s a huge economic contributor to the Commonwealth of Kentucky.
The two conveyor systems Alba supplied are used to carry pallets holding up to 200 finished barrel heads.
System #1 Process
ASI supplied a whiskey barrel head char loading, Denso robot and head conveyors. ASI utilized Alba’s pallet dispenser to dispense pallets to a robot loading zone, providing accumulation for incoming heads to work in conjunction with the robot and head conveyors. This allowed ASI’s head rounder to keep making barrel heads even if the whiskey barrel head char is down.
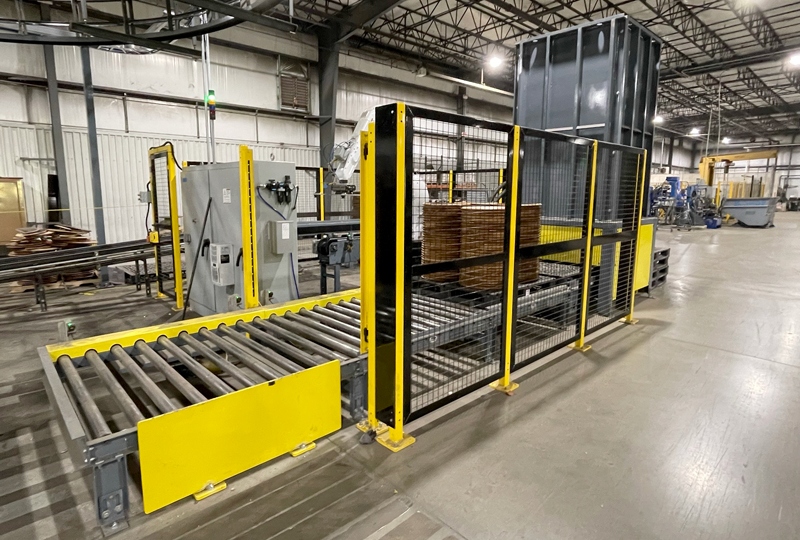
The robot palletizes the whiskey barrel heads to keep the head rounder running. When there are any gaps, the robot removes heads from the pallet and places them in the head char. When the pallet dispenser is empty, the line is reversed. The pallet dispenser now becomes a pallet stacker as it accumulates the pallets back into the stacker magazine.
System #2 Process
The charred barrel heads are delivered from the head char process via an ASI supplied conveyor. Then it accumulates the heads on a zoned accumulation conveyor and loads them onto plastic pallets using the Denso robot equipped with a custom end effector.
As pallets are loaded, they are conveyed to another CDLR conveyor when full. The pallet dispenser dispenses another pallet to start the process over.
The barrel heads are very lightly charred as compared to the rest of the barrel. If the barrel heads are charred too much, the heat bends them out of shape. Picture a burning piece of paper — it folds upwards as it burns. The same holds true for barrel heads — making them impossible to attach to the barrels.3
Biggest Challenge & Solution
Design a system allowing maximum product flexibility in the event the end user’s head rounder or head char equipment didn’t operate properly. Alba provided a system that allowed the end user to both dispense and stack empty pallets with a single unit. Utilizing Alba’s standard center drive equipment, the cell operates in forward and reverse directions – saving costs by avoiding the need for a second unit and saving valuable floorspace.
Conveyor/Product Specifications
Alba supplied two (2) systems to facilitate ASI’s pallet handling needs for their two (2) robotic cells.
System #1 consisted of the following equipment for the Whiskey Barrel Head Char Loading Cell:
- One (1) Pallet Dispenser/Stacker
- One (1) Thru-Frame Transfer, Model TFT 251140-6-3S
- Two (2) CDLR Conveyors, Model 251140-6
- One (1) Frame-to-Frame Transfer, Model FFT 251140-6-3S
System #2 consisted of the following equipment for the Post Whiskey Barrel Head Char Loading Cell:
- One (1) Pallet Dispenser
- Three (3) CDLR Conveyors, Model 251140-6
Value-Added Features
- Special Paint Color RAL 7031 (Blue Grey)
- Adjustable Pallet Back Stops
- Fixed End Stops
About Us
Alba Manufacturing, established in 1973, engineers and designs heavy-duty roller conveyor systems. Our systems consist of chain driven live roller (CDLR), zero pressure accumulation, drag chain, gravity, lift and rotate, pallet stackers and dispensers, turntables, chain transfers and transfer cars. Our corporate office and manufacturing facility is located in Fairfield, Ohio, approximately 30 minutes north of Cincinnati, Ohio.
For more information regarding this application/solution, please contact us via phone at 866.252.2634; via web at www.albamfg.com or via email at RockSolidConveyor@albamfg.com.