Whether you grill’em at a cookout or grab one at a fast-food joint on your way to the beach, hamburgers and summer go together like nothing else. For many of us the sight, sound, and smell of burgers sizzling on the grill, can trigger many of our best early memories during the warmest days of the year.
This case study features a palletizing line in a distribution center for a leading fast-food hamburger purveyor brought to Alba Manufacturing by one of our integration partners, K2 Kinetics, out of York, Pennsylvania. K2 was tasked with designing and building an automated palletizing cell for cartons of product. These cartons needed to be palletized and wrapped prior to being shipped to various distribution channels. Alba’s assortment of pallet handling products served as the material handling basis of K2’s robust and efficient robotic palletizing system.
The process starts with a stack of empty pallets loaded by fork truck into Alba’s robust pallet dispenser. Pallets are then sent one at a time down the transfer line to one of the two palletizing lines.
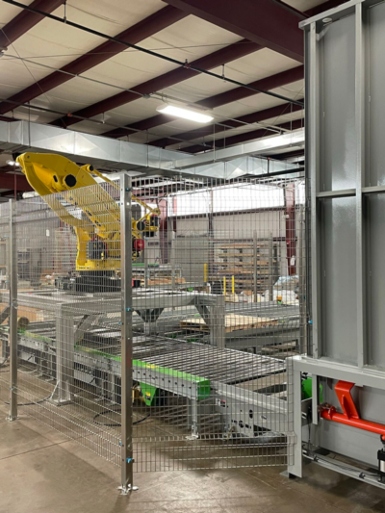
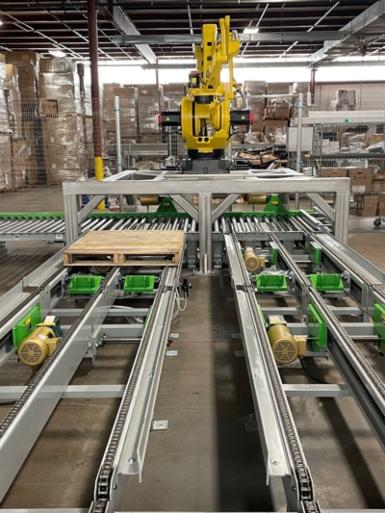
These palletizing zones, consisting of Alba’s standard DC-R80-3S, (3-Strand) Drag Chain Conveyors, including side guides and a pivoting-style pop-up stop locating the pallet’s leading edge prior to palletizing.
Once fully palletized, the CLDR conveyor will convey the fully loaded 1,500 lb. pallet of burger buns to the adjacent 3-strand pop-up transfer, and eventually downstream to the customer-supplied stretch wrapper.
After the full pallet has been stretch wrapped, it accumulates with other pallets down Alba’s CDLR conveyor to a fork truck unload station, where finished pallets are removed from the system and shipped out to fill the needs of hungry customers.
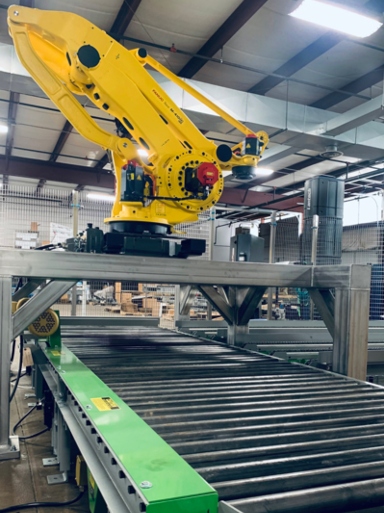
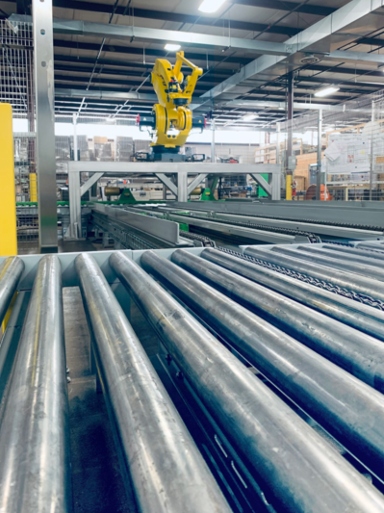
The implementation of Alba’s pallet handling equipment reduced the safety risks and the excessive costs associated with reliance on fork trucks for pallet handling. The new palletizing cell is now able to efficiently automate an otherwise complicated and labor-intensive operation, while the robustness of Alba’s structural steel-constructed equipment ensures the process will continue long into the future.
Conveyor/Product Specifications
PRODUCT: 40″ x 48″ GMA Pallets, 1,500 lb. Maximum (full) and 75 lb. (empty)
Conveyor/Product Specifications for Various Conveyors:
- One (1) Pallet Dispenser, 15 Pallet Capacity, 30 FPM, 18″ TOC (Discharge Elevation)
- Two (2) Model TFT 251140-4, (2-Strand) Chain Transfers, 30 FPM, 18″ TOR, 36″ Chain Centers
- Four (4) Model R80-3S, (3-Strand) Drag Chain Conveyors, 30 FPM, 18-3/4″ TOC, 36″ Chain Centers
- Two (2) Model TFT 251140-4, (3-Strand) Chain Transfers, 30 FPM, 18″ TOR, 18″ Chain Centers
- Model 251140-4 Chain Driven Live Roller Conveyor, 30 FPM, 18″ TOR
Value-Added Features
- End Stops (Fixed and Adjustable)
- Backstops
- Blade Stops (Pneumatic)
- Side Guides
- Fork Truck Barriers
- Fork Truck Wheel Stops
- Color Match Paint Scheme
About Us
Alba Manufacturing, established in 1973, engineers and designs heavy-duty roller conveyor systems. Our systems consist of chain driven live roller (CDLR), zero pressure accumulation, drag chain, gravity, lift and rotate, pallet stackers and dispensers, turntables, chain transfers and transfer cars. Our corporate office and manufacturing facility is located in Fairfield, Ohio, approximately 30 minutes north of Cincinnati, Ohio.
For more information regarding this application/solution, please contact us via phone at 866.252.2634; via web at www.albamfg.com or via email at RockSolidConveyor@albamfg.com.