Auto racing or automobile racing is one of the most well-known competitions in Motorsport. Annually, auto racing in the U.S. and around the world attracts millions of live-event spectators and household viewers. Team sponsors smartly capitalize on viewership to sell and market their products. The global market for Motorsport, which was predicted to be worth $4.8 billion in 2021, is expected to expand to $7.8 billion by 2026.1
One of these sponsors, who manufactures a line of lubricant products, partnered with Equipment Depot | EQSolutions on a conveyance project. At one of their distribution facilities, they needed to accumulate full pallet loads of product via several inbound receiving lines as pallet loads were incoming from another building on their premises.
Three distinct types of pallets needed to be staged on conveyor lanes for AGV (Automated Guided Vehicle) pick-up at the discharge ends. Pallet loads (up to 2,500 lb.) would be dropped off by fork truck on the conveyor lanes’ infeed ends. After staging and pick-up, AGVs would deliver the pallets to racking for storage.
Equipment Depot was especially excited to use Alba’s MZPA conveyor controls to see how this truly plug and play system would streamline their installation, time, and costs.
The end user had a total of six (6) lanes they needed to implement, but only four (4) of those lanes were bought at the onset. Each lane needed to accumulate up to twelve (12) pallets in queue and be ready for AGV pick-up. Alba’s Motorized Zero Pressure Accumulation (MZPA) conveyor was the right fit for this application. The MZPA conveyors are individually motorized Chain Driven Live Roller (CDLR) conveyor zones that are controlled through a series of Programmable Logic Controller (PLC) based, onboard, conveyor-mounted control boxes.
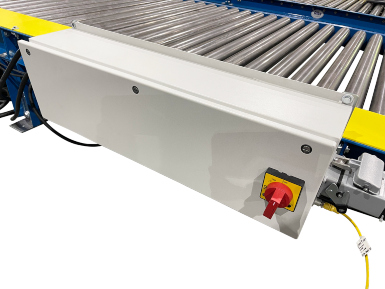
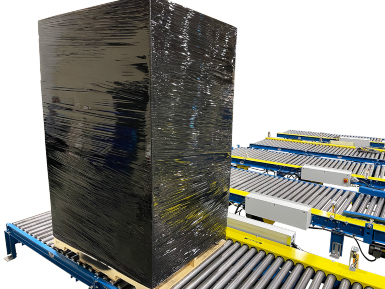
Alba used 3-1/4″ roller centers because the pallets were traveling the hard way (meaning the bottom boards were oriented parallel to rollers) and would convey effectively on a tighter roller center. Each zone has a single photo-eye to sense if product is present. The fork truck drop-off zone and the AGV pick-up zone were also outfitted with an ultrasonic sensor. It detected vehicle interface and would automatically start or delay conveyor movement within the Alba programming based on where those vehicles were and the pallets’ location within those zones.
Each zone’s photo-eye, sensors, and motors are wired via a Quick Disconnect (QD) cable back to the control box. The control boxes can control up to four conveyor zones. Each line had multiple control boxes that were wired via QD cables to connect each box together. One (1) 460-volt power drop was supplied to each lane of conveyor by Equipment Depot in the field.
All conveyor lanes were fully tested and ran automatically in Alba’s facility prior to shipment to ensure flawless operation. Alba shipped all lanes in individual sections after rolling the corresponding QD cables back up to each control box for ease of shipping. This made it remarkably simple for the installer to unroll and plug each cable back in to the right control boxes in the field.
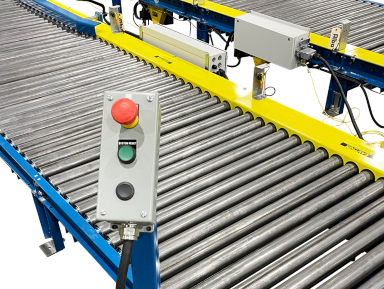
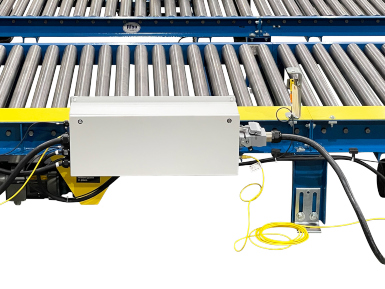
Alba shipped all the sections pre-assembled with leg supports making it a quick truck-to-site installation. Equipment Depot collaborated diligently with Alba and the end user to provide a solid solution and a means to facilitate conveyance in a simple manner that was easy to install, but also very reliable and rock solid.
The end user was incredibly happy after the installation. Our partner, Equipment Depot was thrilled by how quickly the system was up and running with minimal effort.
With a second phase and two more lanes needed, there is still more work to come!
“The four-lane system was complete in just 2-1/2 days! We’re so surprised how quick the install was and honestly it could not have gone any smoother.”
– Customer
Conveyor/Product Specifications
- 4 Lanes of Model MZPA251140-3.25 Motorized Zero Pressure Accumulation CDLR Conveyor 59′ x 3″ Long
- Each Lane Consisting of Twelve (12) Zones @ 4′ x 11-1/4″ Long Each
- Each Zone is Individually Motor Driven via 1/2 HP Baldor Motor
- 44″ Effective Conveying Width
- 2-1/2″ Diameter x #11 Ga. Rollers with 11/16″ Spring-Retained Hex Axles
- 3-1/4″ Roller Centers
- RC40 Chains Roll-To-Roll
- Bearings, Grease Packed
- Rollers Set 7/8″ Low (Drive Side) & 1/4″ High (Non-Driven Side)
- Under Slung Drive with Double Single Driver Sprocket
- Controls included Alba’s Plug and Play MZPA Zone Control System with Allen Bradley Micro 830 PLC
- Each Zone Included Banner Retro-Reflective Photo-Eyes
- Load and Unload Zones Included Banner Ultrasonic Sensors
- Primary Power was 460 Volt/3 Phase/60Hz.
- Control Power is 24VDC
- Speed: 45 FPM, Fixed
- Elevation: 18″ Top of Roller
- Thirteen (13) Adjustable Supports per 59′ x 3″ Section
- Paint: Alba Blue & Safety Yellow Guards
- All Drawings Completed by Alba in 3D STP File Format
About Us
Alba Manufacturing, established in 1973, engineers and designs heavy-duty roller conveyor systems. Our systems consist of chain driven live roller (CDLR), zero pressure accumulation, drag chain, gravity, lift and rotate, pallet stackers and dispensers, turntables, chain transfers and transfer cars. Our corporate office and manufacturing facility is located in Fairfield, Ohio, approximately 30 minutes north of Cincinnati, Ohio.
For more information regarding this application/solution, please contact us via phone at 866.252.2634; via web at www.albamfg.com or via email at RockSolidConveyor@albamfg.com.