In the dynamic landscape of food production, efficiency and reliability are paramount. When a major food group provider sought to enhance their manufacturing process with the addition of robotic palletizing lines, they turned to Alba Manufacturing and integrator APT Manufacturing Solutions for an innovative solution. This food group specializes in food products for the food service, retail, and K-12 school service arenas.
The Challenge
Each robotic palletizing line required two pallet conveyors to allow the robot to continue building a unit load on one pallet conveyor while a finished unit load transferred out of the robotic cell onto an outbound trunkline on the other pallet conveyor.
A great Alba integration partner, APT Manufacturing Solutions, reached out to Alba to provide a pallet conveyor solution for the challenge of feeding two different pallet types to these four new palletizing lanes in a tight space as part of a new building expansion. APT integrated Alba equipment into their MOD-PAL® palletizing system along with the case infeed conveyor, palletizing robots, and the stretch wrapper as well as the electrical integration and installation.
One of the challenges of this project was to provide two automatic empty pallet dispensers in line with the single trunkline that fed empty pallets to the robotic palletizer lanes. The customer’s case product SKU determined the type of pallet (GMA or CHEP) for the unit load to be built on.

The Solution
First, Alba designed and provided a standard empty pallet dispenser that would feed a single empty CHEP pallet downstream. Secondly, the next pallet dispenser would need to be a pass-thru style dispenser capable of both conveying that CHEP pallet through itself and dispense a GMA style pallet from its magazine downstream as well (not simultaneously, of course). Third, the system had to be designed to allow for both dispensers to run all CHEP in both or all GMA in both.
Alba relied on standard equipment and excellence in engineering design to facilitate this hybrid use of dispensers in this manner. Once a particular pallet type is dispensed, it is then conveyed to one of four palletizing lanes by use of Alba’s standard 2-Strand Pop-Up Transfers. After a pallet is diverted 90° on the transfer, it travels to the MOD-PAL® robot cell which is protected by wire fencing and then onto two inline CDLR (Chain Driven Live Roller) Conveyors.
The first conveyor is for queuing a pallet prior to the robot loading the empty pallet with sealed cases of food product. The second conveyor is for the pallet build zone complete with locating blade stop and side pusher for the empty pallet. This zone is where the robot palletized the empty pallet with cases of frozen food product. Once palletized, the full pallet then conveys onto a 3-strand drag chain conveyor downstream on demand and out of the robot cell through a light curtain towards the outbound trunkline.

The full pallet trunkline then transfers the completed pallet loads from the palletizing lane 90° on 3-strand transfers downstream to a stretch-wrapper where the palletized product is tightly wrapped together to the pallet, labeled, and ready for outbound freight to the food distributor.
Before the full pallets can convey downstream from this trunkline to the wrapper, the pallet loads needed to be shifted over due to the offset in centerlines between the trunkline conveyor and the wrapper equipment itself. This is because the wrapper is much wider than the conveyor and the tight available space between this equipment, the aisleway, and the building wall.
Alba developed an ingenious solution to use a wider in-frame transfer to pop-up the full pallet and shift it over to match the centerline of the wrapper equipment, thus saving space and enabling a fully functioning system in the space available.
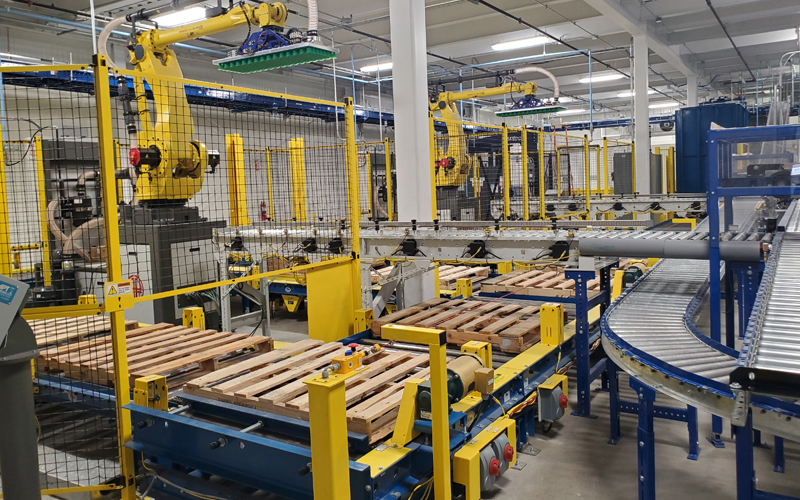
The Results
Our partner, APT Manufacturing Solutions, is thrilled with this heavy-duty robust system, how it functioned, and is proud to provide such a solution to this end user. The end user is very satisfied and continues to efficiently dispatch truckloads of product out the door at a rate of 3,200 cases per hour to distributors each day.
Conveyor Products/Specifications
- 40″ x 48″ GMA & CHEP Pallets
- 2,500-lb. Pallet Loads
- Conveyors Subject to Normal Plant Environment at 40°F
- Two (2) Empty Pallet Dispensers with Devices Pre-wired Back to Enclosure with Terminal Strips
- Various Model 251140-6-52 CDLR (Chain Driven Live Roller) Conveyors for Empty Pallet
- Various Model TFT251140-6-2S-52 Thru-Frame Type 90° Transfers (some with Blade Stops)
- Various Model 2551140-3.25-44 CDLR (Chain Driven Live Roller) Conveyor for Palletizing Lane. Some with Blade Stops and Side Crowders for Empty Pallets
- Various Model DC-R80-3S Drag Chain Conveyor for Full Pallet
- Various Model 251140-4-52 CDLR (Chain Driven Live Roller) Conveyors for Full Pallet
- One (1) Model IFT29740-4-3S-78 In-Frame Type 90° Transfer (with Blade Stop & Backstop) for Shifting Trunkline Centerline inline with Wrapper Equipment Centerline
About Us
Alba Manufacturing, established in 1973, engineers and designs heavy-duty roller conveyor systems. Our systems consist of chain driven live roller (CDLR), zero pressure accumulation, drag chain, gravity, lift and rotate, pallet stackers and dispensers, turntables, chain transfers and transfer cars. Our corporate office and manufacturing facility is located in Fairfield, Ohio, approximately 30 minutes north of Cincinnati, Ohio.
For more information regarding this application/solution, please contact us via phone at 866.252.2634; via web at www.albamfg.com or via email at RockSolidConveyor@albamfg.com.